How to build hanging shelves with integrated lighting, Part 2: Installation
Shelves like these require careful planning and measuring, then measuring again, then testing your measurements, then testing again.The soapstone counters are in, the backsplash tile’s grouted, and our clients will officially move back into their kitchen this weekend. This set of shelves above the sink combines storage and display area with practical illumination while subtly defining the kitchen as its own space, relative to the living room and entry.
It looks simple — and it is. But as is so often the case, achieving a serenely simple look took considerable effort and skill. Here’s how we handled the installation.
1. Support and special equipment
It’s extremely important to have adequate support at the ceiling. If you’re able to design your shelves to hang directly from ceiling joists (or roof rafters), great. If not, you’ll need to add blocking. (See “Better Cabinet Blocking” courtesy of Fine Homebuilding.) The general contractor on this job, Mark Longacre Construction, installed blocking for these shelves when the ceiling was opened up for insulation.
A laser level is an asset for this type of installation, which relies on consistent and precise location of parts. You will also need a hole saw of the right diameter for the light fixtures you’re using.
2. Method
The wire for the lamps in the lower shelf comes up from the basement through the wall. (See the wire poking out of the hole, left of the cabinet?) We had carefully determined the location for the wire before drywall installation. The kitchen side of both hanging shelves will be screwed against the side of the cabinet here, for extra support, so we began the installation by referencing off the cabinet.
To start, John and Mark cut support blocks to hold one of the shelves at the lower-shelf height. When determining the vertical position of hanging shelves, it’s important to bear in mind the heights of those who will be using the kitchen; you don’t want the shelf to be right at their eye level, blocking their view, but a little higher, affording an unobstructed view into the room beyond. Note that we clamped the supports to the wall to keep things steady and also screwed a temporary support of scrap wood to the wall to hold the shelf at the far end.
Had we been installing to a flat ceiling, we would not have had to add angled supports. (An alternative would be to use gimballed nuts.) In this case, the sloped ceiling is just the rafters’ width from the roof.
For these shelves, which have an outside frame of solid oak that will bear the weight of the shelves and their contents, it was critical that we drill the holes for the rod in the center of the solid frames’ width. We used a laser level to mark the location of these holes at the ceiling, to guide the position of each ceiling cleat.
With one hole marked on the ceiling, John and Mark used a roofing square to extend the location to the other side of the shelf.
They screwed the ceiling cleats in place temporarily.
With the first shelf set firmly in place (here, against the wall and cabinet), use the laser level to locate the drilling for the threaded rod in the ceiling cleat and one of the shelves.
Cut the holes for the lamps. We used a hole saw on a drill. (See next image.)

It’s very important to drill the holes perpendicular to the shelves and in perfect alignment with each other, from the top shelf to the bottom. Mark clamped the shelves together with the wall end of each one flush (at the left end, above).
John removed the cleats from the ceiling and Mark drilled them. First he counterbored a hole large enough to accept the nut at the top (when the rod was threaded in for the final time, we added thread locker to keep the rod from coming loose — not that that’s likely to happen, but still…). Then he drilled a hole just a tad larger than the diameter of the rod through the bottom face of the cleat.
After inserting the rods (still over-length) through the ceiling cleats so they bottomed out flush with the end of each nut, Mark screwed the cleats back in place temporarily.
We set the top shelf in place, leveled it, and ran nuts up to its underside to hold it. Then we repeated this sequence with the lower shelf. This way we knew we would get accurate lengths for the oak tubing that would slide over the rod and hide it. (Note that the rod is still over-length. We didn’t want to cut it to length until we had the whole thing put together finally.)
Now it was time to cut the oak tubes to length. Because this ceiling is sloped, the upper sections of oak tubing were different lengths from one part of the shelf to the other. I marked each piece with an identifying letter (A and D here) and a “t” for top or “b” for bottom, to ensure we kept the grain continuous for each piece.
We took the shelves back down and slid the oak tubing over each section for the top shelf, then taped each piece in place to hold it temporarily.
With the top shelf in place, we threaded on the nuts and checked the shelf with a level, making micro-adjustments until everything hung just right. Once the nuts are under tension from the weight, they’re going nowhere.
We slid the lower sections of oak tube over the rods and held them temporarily with tape. Then we put the lower shelf up temporarily one last time, just to check that everything was right. This also allowed us to mark the precise point at which to trim the rod to length.
We used acorn nuts to hold the lower shelf in place — they’re a lot better looking than regular nuts. But they also have a finite capacity for the threaded rod, so we threaded a scrap of rod fully into one acorn nut, marked its top edge, then added that measurement (it was about 1/4 in.) below the mark we’d made on each rod for the underside of the shelf.
We took the shelf down one last time (phew!), then John cut each rod to length with a battery-powered reciprocating saw. Mark held the rod to minimize the vibration.
After electrician Isaiah Merriman installed the lamps, we realized that the cavity in the lower shelf wasn’t quite tall enough to accommodate the transformers. (I hadn’t had a transformer at the start of this odyssey; I only had the lamp.) We needed another 1/4 in. of height. I could have made a thinner shelf and shimmed up the support fillets (see part one of this series), but I’d already made and finished a nice white-oak-veneered shelf that was 3/4 in. Another option would have been to build up the fillets and add a veneered oak edge to the shelf to conceal the little bit that would protrude over the top edge of the solid oak frame. I didn’t want to do that, because I like knowing that objects placed on the shelves will be safer if the solid frame stands a little higher than the top face of the shelf.
My solution was to measure for the position of each transformer and mark these locations on the underside of the shelf insert. I then took the shelf outside, lay the finished upper surface on a protective blanket, and used a router with a straight cutter to hog out a recess. I made each recess oversize, knowing from experience that if I didn’t, one or more would certainly not fit, and I’d have to wrestle the whole thing out again and re-rout it.
Getting the removable shelf in place was a trick; it would only fit in through the far end, and I had to be careful to avoid damaging the cabinets on that wall. But in it went, and with a little jiggling, it settled right into place.
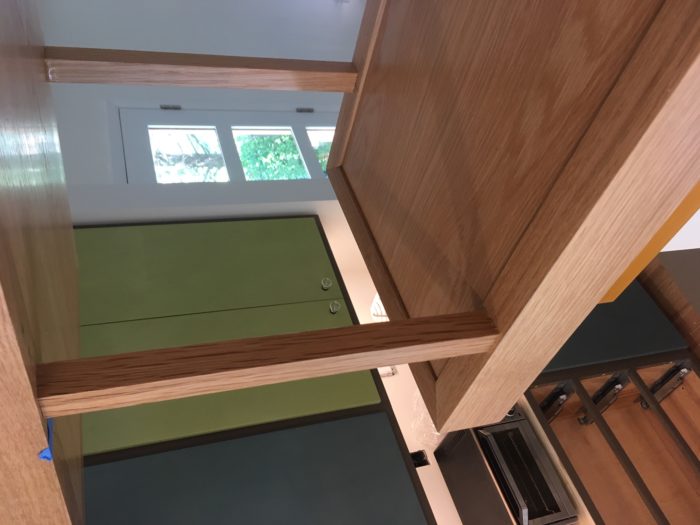
The shelves with their lamps installed and the ceiling cleats painted white.
-If you’re even thinking about remodeling a kitchen, you need to pick up a copy of Nancy’s new book Kitchen Think. It’s filled with the clever builds you’d expect from someone who has been creating beautiful, high-end kitchens for decades.
![]() |
|
![]() |
|
![]() |
Log in or create an account to post a comment.
Sign up Log in