A Simple Guide to Sawblades
For cleaner cuts, look beyond the basic combination blade.
Synopsis: Most tablesaws come equipped with a combination blade designed to make both crosscuts and ripcuts in a variety of materials. However, those blades don’t excel at any one task, which is why manufacturers make blades designed specifically for crosscutting or ripping, and for cutting chip-prone materials such as melamine-coated plywood. With one of these specialized blades, you can get cleaner cuts with less effort. But before you buy one, you need to understand some basic sawblade geometry, which blades match up to the woodworking you do, and what to look for when buying a blade.
From Fine Woodworking #208
Most tablesaws come equipped with a combination blade designed to make both crosscuts and ripcuts in a variety of materials. However, those blades don’t excel at any one task, which is why manufacturers make blades designed specifically for crosscutting or ripping, and for cutting chip-prone materials such as melamine-coated plywood. With one of these specialized blades, you can get cleaner cuts with less effort. But before you buy one, you need to understand some basic sawblade geometry, which blades match up to the woodworking you do, and what to look for when buying a blade.
Rip blades
Need for speed
Ripcuts are easier to make than crosscuts, so they can have a faster feed rate. To help clear chips, the typical 10-in.-dia. rip blade has 24 teeth, leaving wide gullets between the teeth to accommodate the chips while the tooth is still in the cut. The top edge of each tooth is flat (perpendicular to the plane of the saw plate). Known as a flat-top grind (FTG), it is durable and relatively economical to sharpen. It has the advantage of cutting both sides of the kerf simultaneously, which reduces sawblade stresses and vibration and leaves a cleaner cut.
To accommodate a higher feed rate, the teeth have a hook angle of 20º to 25º, meaning that each tooth leans forward. This helps pull the wood into the blade.
To counteract tearout, many rip blades have low clearance angles that cause the chips to drag on the side of the teeth, creating friction, heat, and residue buildup. If you tend to make one or two ripcuts at a time, this may not matter. But in a production shop, this blade will need cleaning more frequently than other blades. A rip blade will help anyone get cleaner cuts, but where time is money, a rip blade pays for itself very quickly.
Crosscut blades
More teeth mean cleaner cuts
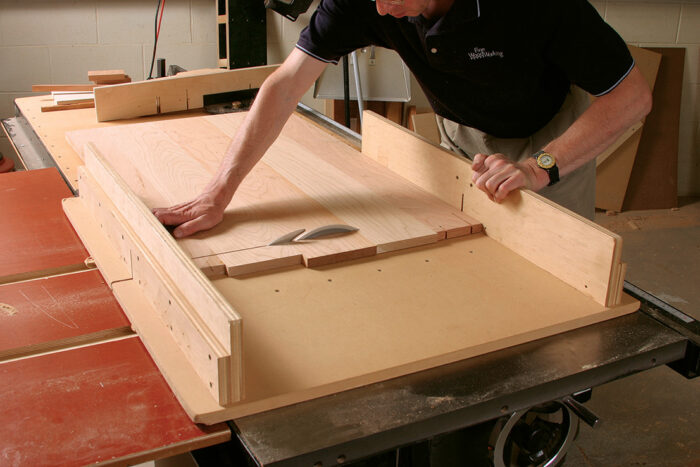
When crosscutting, the problem is not getting rid of chips, but minimizing tearout and chipout. Everything else being equal, while few teeth mean a faster cut, lots of teeth equate to a smoother cut. And the first thing you’ll notice about a crosscut blade is the number of teeth. A typical blade has 80 teeth packed together with only a very small gullet between each one. The hook angle is low—usually in the 5º to 15º range—to accommodate the slower feed rate used in crosscutting.
The teeth are ground with an alternate top bevel (ATB). One tip comes to a point on one side while the next has its point on the opposite side. This profile allows the teeth to cut with a scoring action, reducing the cutting pressure and almost eliminating tearout.
Laminate blades
Eliminate chips in Man-made materials
When cutting brittle surfaces, such as veneered plywood, laminates, or phenolic plywood, even an ATB crosscut blade has trouble preventing tearout. To cater to this need, manufacturers offer two modified versions of the ATB blade. One, called a high ATB, has teeth ground to a higher bevel angle, around 40º. The other has teeth ground to an angle on their tops and on their faces. With this alternate top, alternate face (ATAF) grind, you get a sharper, more pointed cutting edge to slice the most brittle materials.
You also can get a blade with a triple-chip grind (TCG). The first, or lead tooth, has a 45º bevel on each corner that leaves a kerf with sloped corners. This is followed either by a pair of beveled teeth that square up the corners, or by a flat-topped raker tooth ground slightly lower than the lead tooth. In this way, tearout or cracks from the lead tooth are removed by the teeth that follow.
If you work extensively with brittle sheet goods, it is well worth buying one of these specialist crosscut blades. You’ll get a durable blade and clean cuts, and you’ll save wear and tear on your combination blade.
Combination blades
Two great options
Most woodworkers use a combination blade for convenience. But you don’t have to settle for sloppy results. Better blades have a combination grind (also known as a planer combination) that is a mixture of ATB and FTG teeth (40 in all). Four ATB tips cut a kerf with minimal tearout but leave a V-shaped ridge down the middle. A square-tipped raker tooth—slightly lower and narrower than the ATB teeth—follows to remove the central ridge. The raker also helps make cleaner cuts by keeping the blade running straight and square in the cut.
If you work mostly with solid wood, a planer combination blade will fit your needs. But if you mostly use plywood, a Plymaster combination blade is a better choice. This combination blade has 10 ATB teeth followed by a single raker tooth. Although it will crosscut better, it will not rip as fast and freely as other combination blades.
For the full article, download the PDF below:
Log in or create an account to post a comment.
Sign up Log in